Heat Resistance Coating
Heat and corrosion-resistant protection are required in certain extremely severe environments, such as pipework, chimneys, exhausts, furnace, petrochemical industries, or power plants. The temperature might be varied from ambient to 500 degrees Celcius, and the atmosphere containing salt in the offshore area gives a high challenge to the constant maintenance of the steel facilities.
The formulation of heat-resistant coatings based on organic titanium derivatives, particularly butyl titanate, was first described in Heat & Corrosion Resistant Paints by Winter et al. in 1947. Since that time, several developments have occurred, including the use of polymeric butyl titanate and the discovery that alkyl titanates can be used to modify heat-resistant paints based on silicone resins to make them air drying.
Binder selection
Two types of binder give outstanding performance in the temperature range, titanium organics, and silicones. Titanium organics give similar levels of performance to silicones however costs are lower, and paints formulated with them are air-drying. It is usually touched dry within one hour at room temperature and does not require to be heated between coats. The addition of titanium organic to silicone will be able to make the silicone air-drying. When a titanium organic is used as the sole binder, TYTAN™ TNBT, TYTAN™ PBT, and TYTAN™ EHT are recommended. When silicone and titanium organic are used in combination, TYTAN™ TNBT or PBT are recommended for application by brush, but TYTAN™ TNBT is preferred for spray.
Heat Resistance Coating
TYTAN™ PBT has a polymer structure with the chemical formula TixOy(OR)4x-y. TYTAN™ PBT is largely used in formulating heat and corrosion-resistant paints. TYTAN™ PBT can be used with zinc or alumina pigments to formulate paints suitable for application by brush or spray. It can also be used to formulate air-drying paint with silicone resins. The paint contains TYTAN™ PBT and is moisture sensitive during manufacture and storage. The film dries through hydrolysis of PBT to a thin layer of Ti-O-Si and then bonds to the substrate. Once the film has dried, it can stand up to 600 degrees Celcius.
TYTAN™ EHT, tetra 2-ethylhexyl titanate is a titanium alkoxide. TYTAN™ EHT is used in a variety of industrial applications e.g. as an esterification and transesterification catalyst, as an olefin polymerization catalyst, as an adhesion promoter, as a crosslinking agent for hydroxylic compounds, and as a component of heat and corrosion resistant paints.
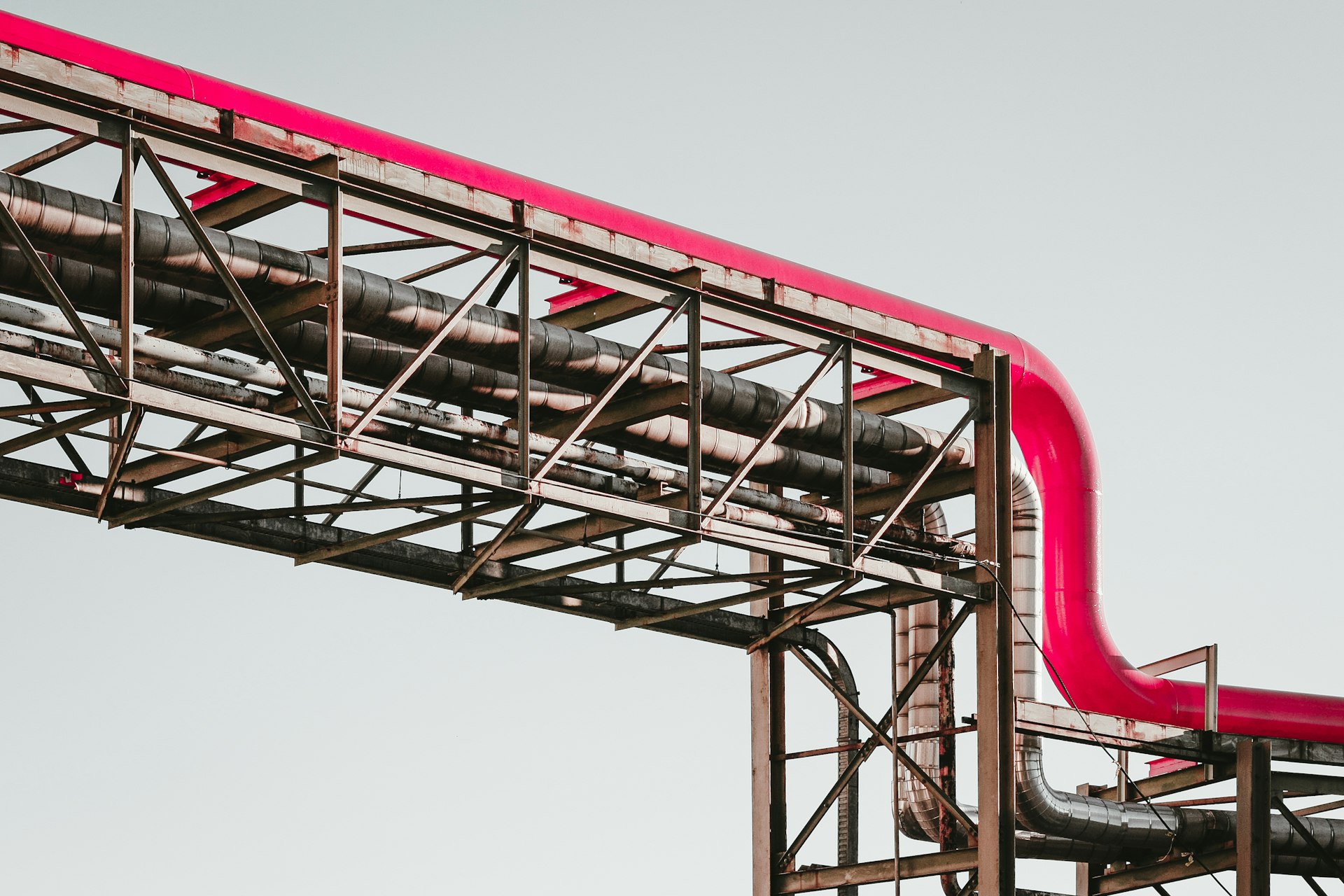
TYTAN™ TNBT is a very reactive primary titanate that will hydrolyze immediately in contact with moisture. It is mainly used as a catalyst for esterification, trans esterification, and olefin polymerization and a very suitable as an adhesion promoting and cross-linking agent for hydroxylic compounds or heat and corrosion resistant coatings. TYTAN™ TNBT can also be used as a moisture scavenger to prolong the shelf life of moisture-sensitive high viscosity products. TYTAN™ TNBT can only be used as an additive to solvent-based products.
To understand more about TYTAN™ applications and benefits please contact our team of professionals at sales@maha.asia.
Want To Know More About Our Solutions?
We Offer A Wide Range Of Ingredients For Surface Technology Formulations!